Table of Contents
- Understanding the Scale and Challenges of Utility Infrastructure
- Handling Operational Complexity Through Intelligent Workforce and Asset Management
- osapiens CMMS: fully connecting your workforce
- How osapiens CMMS integrates with ERPs, GIS systems and any other system:
- The business impact from osapiens CMMS
- Success story: Nordex
- SAP integration going forward
For utility companies, maintaining infrastructure requires highly sophisticated processes. They need to manage workforce operations, work orders, and asset maintenance across multiple systems.
However, many existing digital maintenance systems don’t meet these needs:
- They’re outdated, fragmented, and hard to use for technicians.
- They require expensive and lengthy implementation projects.
- They have steep learning curves, making technician training a challenge.
Utilities need a fully SAP-integrated, automated, and mobile-first approach across all key processes: workforce management, meter management, GIS mapping, and infrastructure maintenance. This is where osapiens CMMS comes in.
In this article, we’ll explain how osapiens CMMS integrates and manages all your data together in one place, allowing energy providers to use their existing SAP systems more effectively.
Understanding the Scale and Challenges of Utility Infrastructure
Utility companies operate on an extensive scale, managing highly complex and distributed asset networks. These networks span thousands of kilometers and include critical infrastructure elements across power, water, and gas sectors.
In power distribution, the infrastructure extends from high-voltage transmission lines and substations down to local transformers serving residential areas. Water utilities manage pipelines connecting centralized treatment plants with local pumping stations and service lines. Gas distribution systems consist of high-pressure transmission lines, city gates, district regulators, and service connections, all requiring precise control and maintenance.
This infrastructure is characterized by a multi-level hierarchy:
- In power, from transmission grids to neighborhood-level distribution
- In water, from treatment facilities to end-user delivery networks
- In gas, from high-capacity pipelines to localized pressure zones
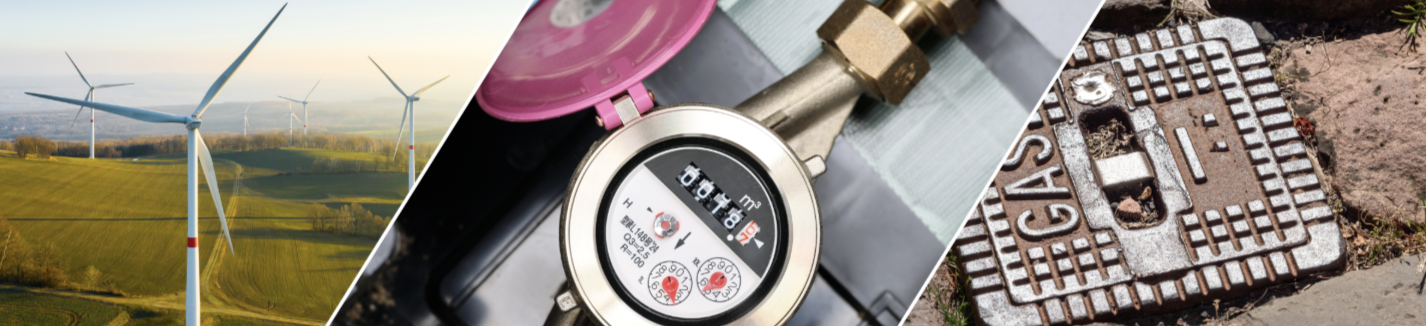
Assets within these networks are geographically dispersed and include a wide range of equipment types. For electrical systems, this includes switches, capacitors, and reclosers. Water utilities maintain valves, pumps, and flow meters. Gas networks involve valves, regulators, and meters too.
Operational complexity is further increased by the coexistence of legacy infrastructure with newer, technology-driven systems. Many utilities are in the process of integrating smart grid components, advanced metering infrastructure (AMI), and remote monitoring systems into existing asset bases.
In parallel, workforce and technology challenges continue to mount.
A significant share of the existing utility workforce is approaching retirement age, placing institutional knowledge at risk. According to research from 2023, 56% of utility employees now have fewer than 10 years of experience, highlighting a major generational shift.
At the same time, modernization initiatives are driving the adoption of more complex IT and OT architectures, requiring seamless integration between traditional enterprise systems and newer IoT, analytics, and customer-facing platforms.
This evolution also brings a widening skills gap. Utilities face ongoing difficulty in recruiting and training technicians with the combined expertise needed to operate, maintain, and optimize both conventional infrastructure and new smart technologies.
The result is a hybrid operating environment requiring sophisticated maintenance strategies, high asset visibility, and integrated planning tools to ensure uptime, safety, and compliance. With the right software, utility providers are able to transform their operations.
Handling Operational Complexity Through Intelligent Workforce and Asset Management
These complex challenges that utility companies face demand a better, more efficient maintenance approach. Here’s how osapiens CMMS can transform utilities maintenance:
Workforce management
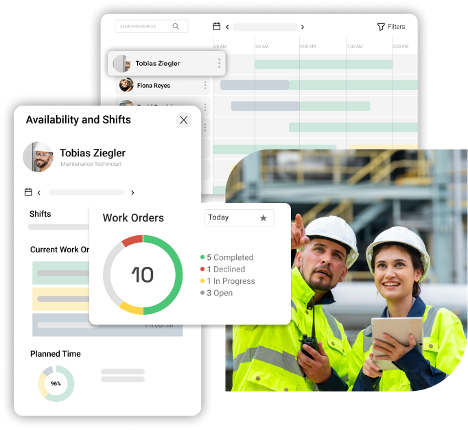
- Intelligent scheduling and dispatching: Automatically assigns technicians based on location, skills, and priority levels. The system can manage both standard planned maintenance and high-priority emergency work through dynamic task prioritization.
- Field connectivity and mobile solutions: Provides real-time access to work orders, digital checklists, and asset information, even in remote areas with offline capabilities.
- Skills-based resource allocation: Matches technician qualifications with task requirements, especially important for high-voltage work requiring specialized certifications. The system tracks certification expiration dates and ensures only qualified technicians are assigned to specialized tasks.
Meter management
- Complete lifecycle tracking: Manages installation, replacement, testing, and decommissioning of traditional and smart meters with full maintenance history.
- Integration with customer data: Connects real-time consumption data with SAP IS-U for accurate billing and customer service, with automated data validation.
- Compliance documentation: Automates records of meter inspections and tests to meet regulatory requirements with built-in validation to ensure all required fields are completed.
Infrastructure asset management and GIS integration
- Asset location and status tracking: Integrates with Geographic Information Systems (GIS) to provide full visibility over transformers, substations, and distribution networks with map-based interfaces.
- Visual damage and fault reporting: Enables technicians to record infrastructure issues with geotagged reports, photos, and precise location data using mobile devices.
- Safety information access: Provides critical details about equipment connections, affected households, and safety protocols for each maintenance task.
- Advanced geographic planning: Supports drawing and editing of geographical areas assigned to different departments, with capacity planning that ensures appropriate skill coverage across all service territories.
Mobile field operations
- Comprehensive mobile workflows: Allows field technicians to execute complex task sequences with smart forms that adapt based on task type and the specific equipment being serviced.
- Offline capability: Ensures continued functionality in areas with limited connectivity, with automatic data synchronization when connection is restored.
- Image and document management: Supports capturing, tagging, and organizing images of assets and work completed, with automatic association to the relevant task or asset record.
- Technical structure access: Provides mobile access to the complete technical structure of facilities, enabling technicians to browse equipment hierarchies and access detailed component information on-site.
Optimized route planning and logistics
- Dynamic routing: Calculates the most efficient routes between tasks, considering traffic conditions, priority levels, and required skills.
- Material coordination: Integrates with inventory systems to give technicians access to necessary parts and equipment.
- Time-sensitive scheduling: Handles tasks that span multiple days with appropriate time allocation and seamless handover between shifts.
With a fully integrated maintenance solution, utility companies can transform how they manage their complex infrastructure, moving from reactive repairs to proactive maintenance that extends asset life and improves reliability – all while maintaining comprehensive records for regulatory compliance.
osapiens CMMS: fully connecting your workforce
osapiens’ cloud-based maintenance platform brings true workforce efficiency to utility companies.
By smoothly integrating with existing SAP systems, it improves maintenance processes:
- Certified SAP connector: With osapiens’ certified SAP connector, integration is out-of-the-box rather than requiring custom development for each client.
- GIS Integration: Providing location-based insights for maintenance planning and execution.
- Bringing multiple systems together: osapiens connects your maintenance operations to third-party contractors, asset manufacturers, and real-time infrastructure monitoring.
Unlike legacy software, osapiens CMMS is designed for rapid deployment. This significantly lowers the total cost of ownership and training efforts.
How osapiens CMMS integrates with ERPs, GIS systems and any other system:
While many maintenance SaaS providers claim they can integrate with SAP, not all deliver this as completely as osapiens.
We have over 10 years of specialized experience with SAP integration processes, and our SAP-certified connector allows for the automatic, secure exchange of data between osapiens CMMS and SAP.
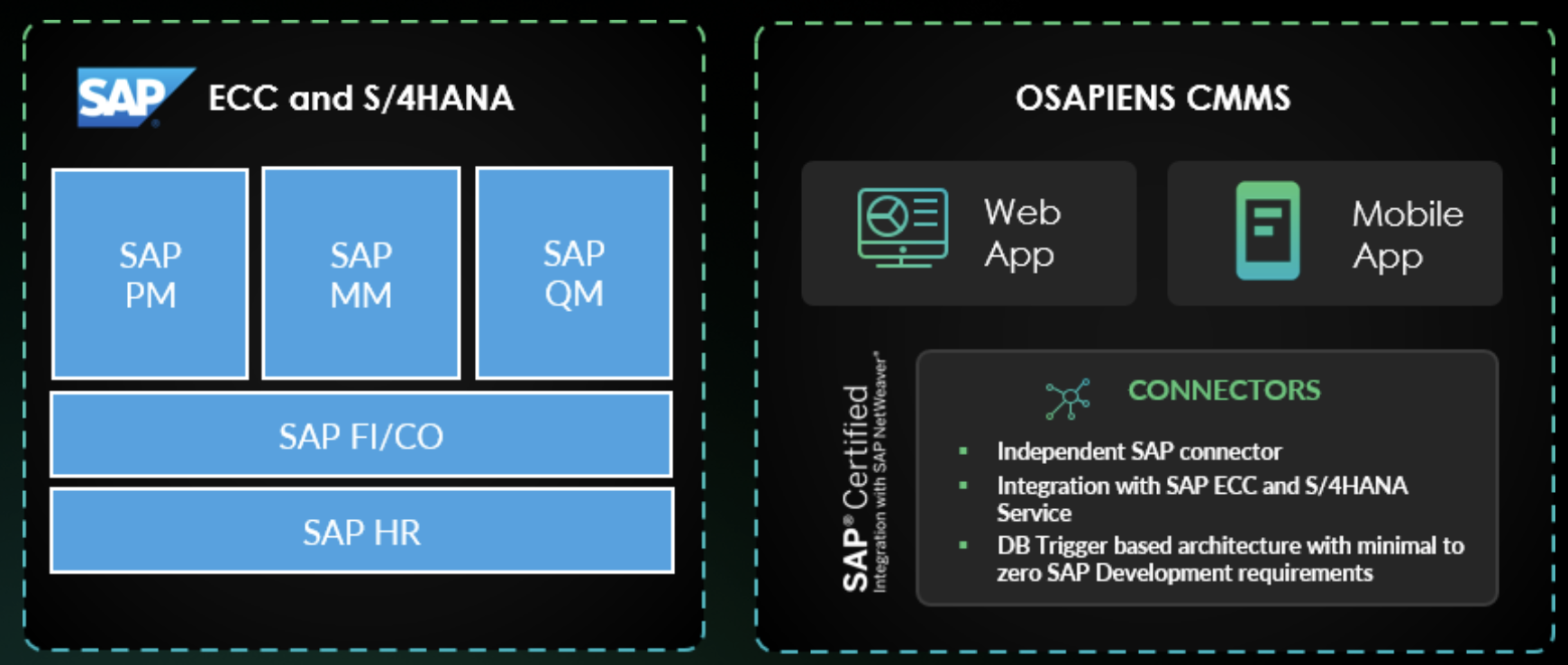
osapiens CMMS is built to integrate all core systems involved in utility maintenance and meter operations — providing one unified platform for planning, execution, documentation, and compliance. Through deep SAP integration and open interfaces, it enables consistent, real-time data sharing across departments and external partners.
SAP Integration (PM, MM, CS, HCM, IS-U)
With its certified SAP connector, osapiens ensures secure, bi-directional data flow across key SAP modules:
- SAP PM (Plant Maintenance): Work order creation, scheduling, execution, and status updates
- SAP MM (Materials Management): Spare parts planning, inventory reservations, and stock updates
- SAP HCM (Human Capital Management): Technician availability, shift planning, and qualifications
- SAP IS-U (Industry Solution for Utilities): Meter and customer data for billing, service orders, and compliance
- SAP FI/CO (Financial Accounting / Controlling): Maintenance-related costs, budgeting, internal controlling, and regulatory reporting
This integration allows for real-time updates between systems, eliminating manual data entry and ensuring data consistency across platforms.
Meter Management and Reading Systems
osapiens supports the complete lifecycle of meters — both traditional and smart — through integrations that enable:
- Installation, maintenance, and decommissioning workflows
- Integration of meter readings into SAP IS-U or third-party platforms
- Automated validation and documentation of meter data
- Scheduling and execution of meter reading visits through the mobile app
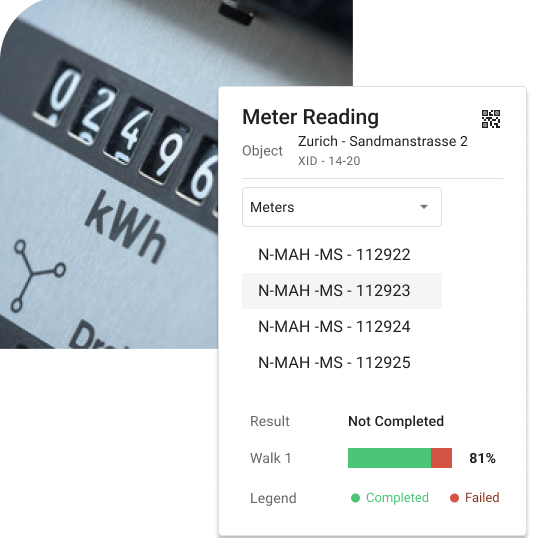
GIS Integration
Combining SAP data with Geographic Information Systems (GIS) is especially critical for utilities. osapiens offers:
- Real-time asset visualization: Integration with GIS systems like ESRI and Smallworld GIS
- Field reporting with geotagged issues: osapiens integrated GIS allows precise asset tracking and maintenance logging
- Spatial analysis for planning: Optimizing maintenance routes and resource allocation based on geographic data
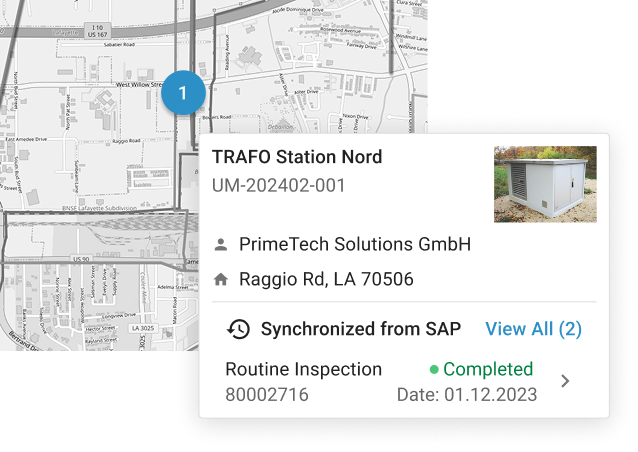
API for Custom Integrations
Beyond standard integrations, osapiens provides a documented developer API (REST) that allows for:
- Custom integrations with specialized utility systems
- Connections to contractor management platforms
- Integration with emergency response and outage management systems
- Communication with control centers for coordinated operations
This flexible architecture ensures that osapiens can adapt to the unique integration needs of each utility, connecting smoothly with both legacy systems and modern cloud platforms.
The business impact from osapiens CMMS
The greatest ROI comes from not just digitization, but fully integrating a modern SaaS solution with existing systems – and osapiens does this better than anyone else.
Adopting osapiens on top of your SAP system provides these benefits:
- Increased efficiency: Faster work order completion, reduced downtime, and optimized resource allocation.
- Cost reduction: Minimizing maintenance costs through predictive insights that prevent breakdowns before they occur.
- Error reduction: Eliminating manual data entry errors from misread handwriting or incorrectly entered numbers.
- Automate compliance and documentation: Automate reporting for audits and regulatory compliance through the osapiens platform.
Success story: Nordex
When wind turbine leader Nordex needed better maintenance tools, they turned to osapiens CMMS. It works smoothly with their existing systems, helping Nordex cut paperwork, reduce errors, and work faster across all their maintenance operations.
For technicians working on wind turbines in remote areas, the mobile app provides everything they need: timely alerts about problems, easy access to instructions and part information, and simple ways to document their work. This has helped Nordex fix issues faster and keep their turbines running longer.
“We needed a reliable system to make our work simpler and more efficient,” says Alberto Erce, who leads Nordex’s technology improvements. With all maintenance information in one place, Nordex now responds quickly to problems while following the same clear processes across all their global locations.
Read the complete Nordex success story here.
SAP integration going forward
As cloud environments become more and more widely adopted, smooth integration will become even more important. SAP is moving clients toward cloud solutions, and the future will involve integrating multiple cloud systems.
For utility companies, this means choosing their maintenance SaaS carefully and ensuring their chosen solution integrates fully with SAP and their current tech stack.
This is why osapiens is the best, safest choice here. We’re committed to staying ahead of SAP’s evolving integration requirements and making sure that our utility customers can always connect their systems completely and securely.
Try osapiens CMMS for free today, or schedule a demo to see the integration in action. We help you fully assess what data you need to synchronize between SAP and osapiens, with one of our experts guiding you through this process with a questionnaire.