Many manufacturers still manage spare parts with a patchwork of SAP entries, spreadsheets, and handwritten notes.
The problem? This manual approach is very time-consuming for technicians. Worse still, it leads to inefficiencies and errors that cause downtime. All of this is very costly for maintenance teams.
This article explores the operational and financial impact of disorganized spare parts management. It also shows how manufacturers decrease downtime, inventory costs, and administrative work with a modern, mobile CMMS.
Why spare parts chaos costs more than you think
Even in companies with traditional software systems like SAP, spare parts management often breaks down because of a lack of proper organization, with data visibility and integration lacking.
This makes errors and stock-outs more likely, increasing downtime – which can cost more than 2 million euros per hour for industries like automobiles and pharmaceuticals.
The impact on labour costs is also substantial: Maintenance technicians often spend a long time on administrative tasks related to spare parts management – time that could be spent on other maintenance work.
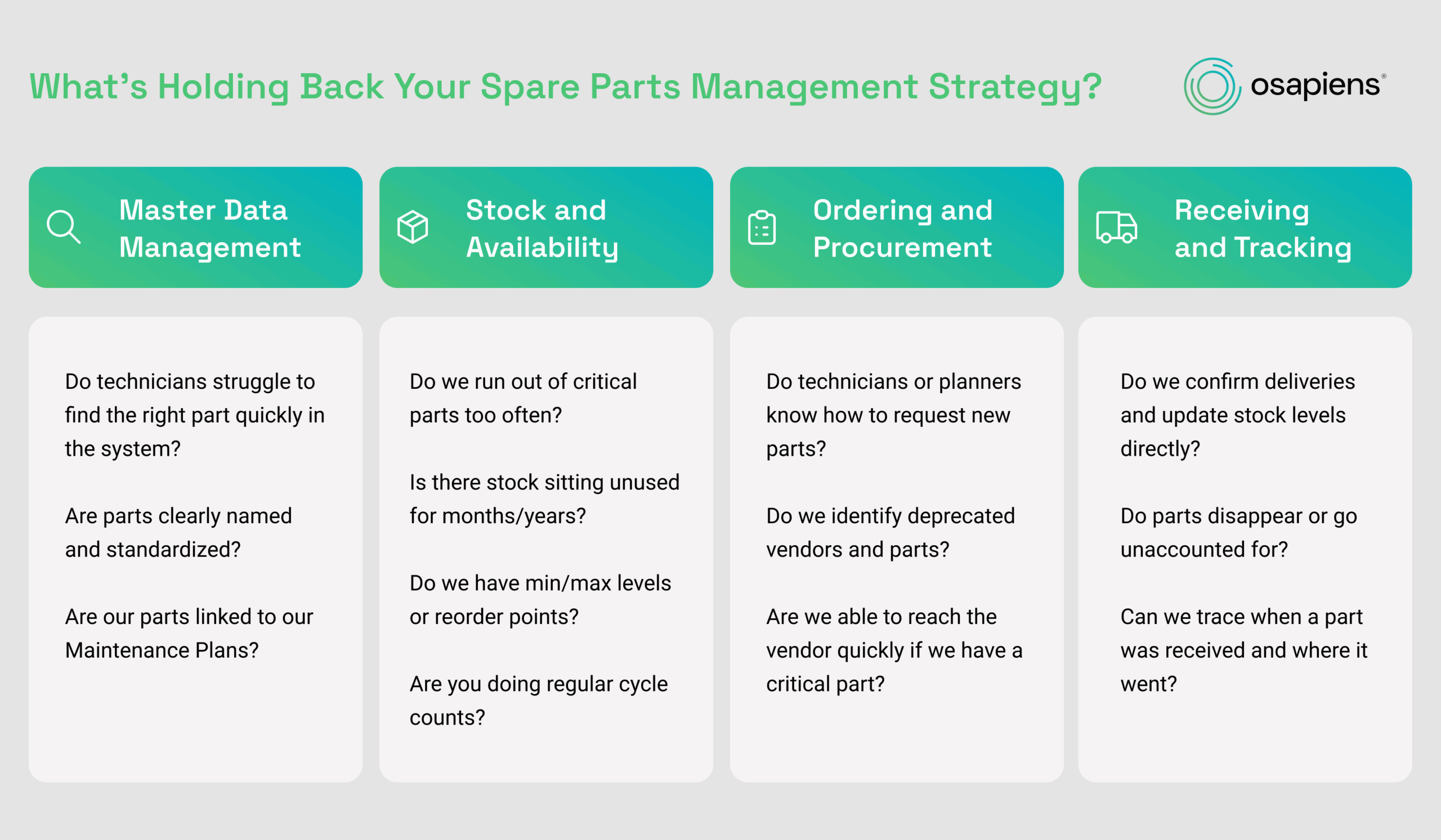
No clear data creates a foundation of confusion
Data quality issues undermine effective spare parts management in several ways:
- Duplicate entries happen more and more across systems, as different sites create their own records.
- Inconsistent naming conventions make finding the right part difficult.
- No linkage between parts and assets leaves technicians without equipment-specific parts lists.
- Missing supplier information complicates reordering when parts are needed.
Without the right data structure, parts catalogs become increasingly unreliable, causing problems throughout the maintenance process.
Poor visibility and access slow down response times
When critical equipment fails, maintenance teams face significant challenges:
- Technicians rely on notes, memory, or emailing procurement instead of direct access to inventory data.
- Lack of mobile access forces shop floor workers to travel to office computers to check availability.
- Parts technically “in stock” may be hard to find in disorganized storage areas.
Inconsistent processes fragment operations
For multi-site operations, spare parts management often lacks standardization:
- Sites and teams manage inventory differently, and SAP is used only partially or inconsistently across locations. No shared playbook exists for best practices across international locations.
- Smaller organizations lack clear ownership for spare parts management.
Without a unified approach, companies miss opportunities to implement best practices consistently throughout the maintenance operations.
Hidden costs beyond downtime
While production stoppage gets attention, poorly managed spare parts create several other financial drains:
- Overstocking ties up capital in slow-moving inventory kept “just in case”.
- Time and effort are wasted on manual tracking and paperwork
- Maintenance quality suffers when parts are unavailable, delaying scheduled work.
Overall, all of the issues we’ve outlined significantly slow down maintenance. They increase the risk of stock-outs, mis-orders, and extended downtime.
A practical approach to fixing it
To restore control, manufacturers need to standardize how parts are catalogued, stored, accessed, and tracked. This is where a modern CMMS becomes a critical tool.
Four core practices for effective spare parts management
1. Clean and structure your data
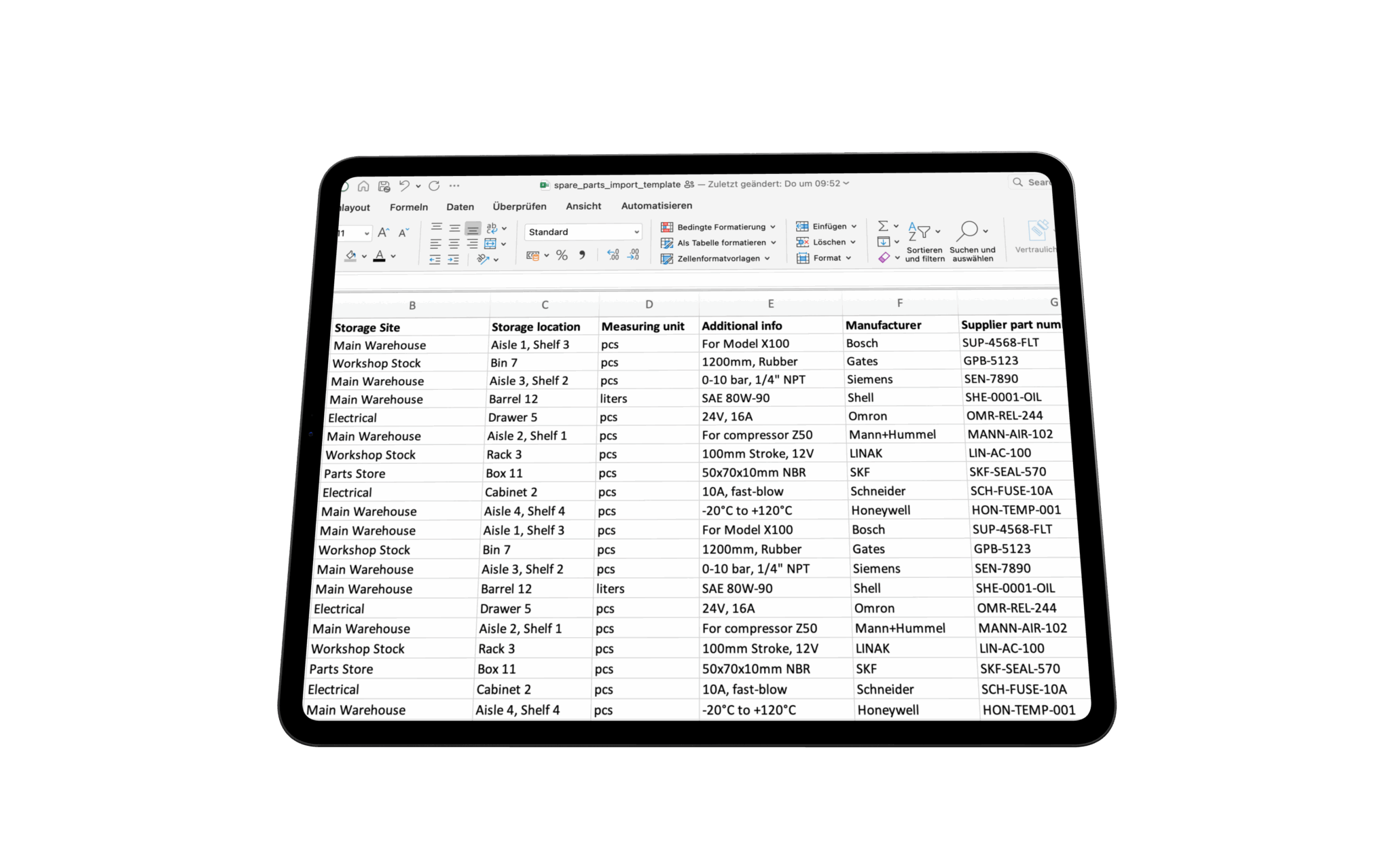
The foundation of any improvement starts with organizing all your parts data in one place:
- Bringing together records from SAP, Excel spreadsheets, and paper-based systems;
- Creating consistent naming conventions and descriptions;
- Removing duplicate entries that lead to confusion and excess inventory.
This initial cleanup phase may seem daunting, but it’s essential for long-term success. Without addressing data quality first, other improvements will have limited impact.
2. Organize your inventory physically
Digital records are only half the solution – physical organization is equally important:
- Assign specific bins or locations for each part.
- Label storage areas clearly with part information.
- Group similar components together for logical access.
- Implement QR codes to enable quick identification and tracking.
A well-organized physical inventory makes parts easier to find and reduces the time technicians spend searching. It also simplifies regular inventory checks and enables more accurate stock keeping.
3. Link parts to specific assets
Creating direct connections between spare parts and equipment delivers multiple benefits:
- Register which components belong to which machines.
- Track usage patterns to identify recurring maintenance needs.
- Quickly identify high-failure components that may need quality investigation.
This approach provides the kind of operational excellence and high-quality data insights that help prevent future failures.
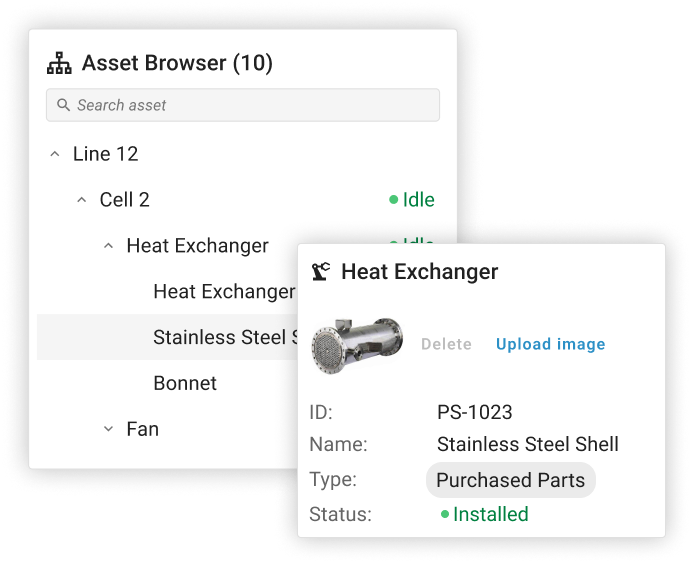
4. See current data instantly
Having visibility over all up-to-date information across maintenance systems ensures decisions are based on accurate information:
- Inventory is updated automatically as parts are used.
- Minimum thresholds are set to trigger reordering before stockouts occur.
- Everything is integrated with procurement systems like SAP for streamlined purchasing.
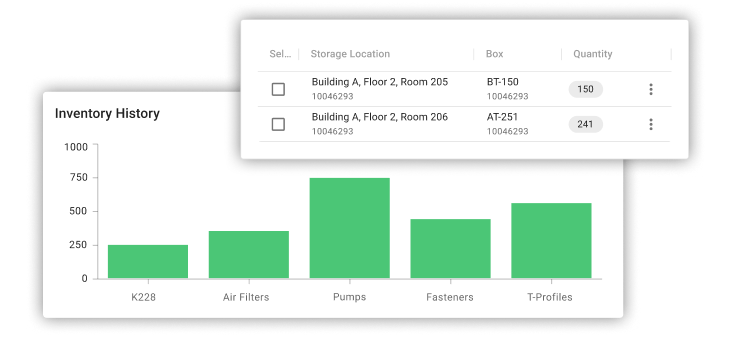
These best practices make life easier for technicians and lead to better-functioning maintenance teams. They reduce unplanned downtime, improve maintenance KPIs, and enable better cost control across the organization.
How osapiens CMMS cuts administration while improving control
osapiens CMMS is designed to help maintenance teams bring efficiency and control to spare parts management, significantly reducing downtime, inventory costs, and administrative effort.
Simplified data management with a single source of truth
The platform makes it easy to establish and maintain a reliable parts database:
- Easy onboarding via Excel imports lets you transfer existing spare parts data using simple spreadsheet templates
- One-scan updates for inventory movements eliminate manual data entry
- Automated stock level tracking maintains accurate counts as parts are used
This approach makes even large-scale data clean-up projects manageable. You can consolidate information from multiple sources without the complexity of traditional software implementations.
Mobile-first access for technicians
At osapiens, we recognise that maintenance happens on the shop floor, not behind a desk:
- QR code scanning enables instant identification of parts and storage locations
- Visibility of stock in real-time from anywhere in the facility eliminates unnecessary trips to check availability
- Work order integration allows parts consumption to be logged during maintenance tasks, not as a separate administrative step
This mobility substantially reduces time spent by technicians on non-productive tasks, allowing them to focus on actual maintenance work rather than paperwork.
Smart integration with existing systems
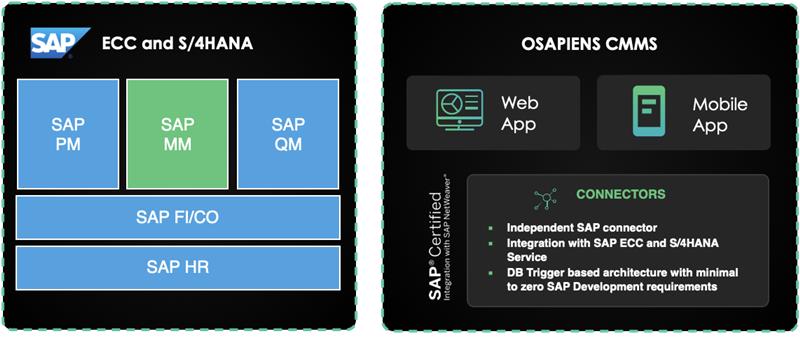
osapiens CMMS works alongside your current infrastructure:
- Supplier data stored at the part level provides quick access to vendor information
- Integration with SAP for material and procurement processes maintains financial control
- Planned purchase order functionality (coming Q3 2025) will streamline the ordering process
This balanced approach works with the software like SAP you may already have, while adding specialized features that maintenance teams need for daily operations.
Cost and performance visibility
Beyond daily operations, osapiens CMMS provides insights for continuous improvement:
- Up-to-date stock valuation tracking helps optimize the amount of funds tied up in inventory
- Usage trend analysis by part, asset, and site informs smarter stocking decisions
- Supplier performance monitoring makes it easier to manage and assess your vendors
With a consistent structure in place and live access to the right data, technicians can work faster, downtime is reduced, and spare parts become a source of insight – not confusion.
Ready to transform your spare parts management?
Your maintenance team is already fighting downtime, equipment failures, and production pressures. They shouldn’t have to fight their spare parts system, too.
Book a personalized demo to see how osapiens CMMS can help you manage your spare parts effectively, reducing stockouts, downtime, and time-consuming admin – laying the groundwork for smarter, more connected maintenance across your organization.