Table of Contents
- What are the benefits of a CMMS? What problems does it solve?
- 1. Better data management unifies scattered maintenance information:
- 2. Streamlined work order processing eliminates inefficient planning
- 3. Real-time inventory management prevents stockouts and overstock
- 4. Preventive maintenance reduces unplanned downtime and failures:
- 5. Automated documentation simplifies regulatory compliance
- The essential features of a CMMS
- CMMS in practice: industry examples
- Looking forward: exciting innovations in CMMS solutions
- Making the right choice of solution
- Why choose osapiens HUB for Maintenance
Maintenance teams today face increasing pressure to reduce downtime, extend the life of assets, and improve their efficiency – all while keeping costs under control. But relying on spreadsheets, paperwork, and other outdated ways of working often makes it harder to achieve these goals.
This scenario plays out in factories and facilities worldwide, but it doesn’t have to. A Computerized Maintenance Management System (CMMS) exists to prevent exactly these kinds of situations.
A CMMS is a software that centralizes and automates many aspects of maintenance operations. By creating efficient digital workflows, a CMMS helps organizations move from reactive firefighting to effective maintenance management. Let’s explore how a CMMS works and the key benefits it brings to modern maintenance teams.
What are the benefits of a CMMS? What problems does it solve?
At its core, a CMMS transforms maintenance operations by replacing manual, paper-based processes with much more efficient digital workflows.
1. Better data management unifies scattered maintenance information:
- A CMMS serves as your single platform for maintenance data. Teams can quickly search and filter through thousands of assets, access complete maintenance histories, and communicate in real-time.
- All critical information is stored, updated, and accessible in one place. This makes it easy to track performance, spot trends, and make informed decisions about maintenance strategy.
2. Streamlined work order processing eliminates inefficient planning
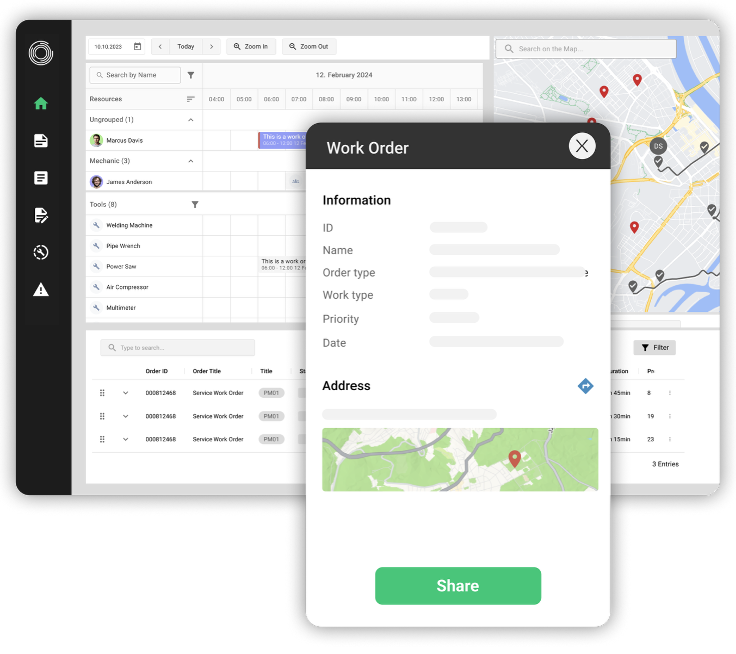
- Smart checklists guide technicians through maintenance tasks, ensuring work is completed correctly and safely.
- Maintenance requests can be easily submitted and converted into detailed work orders using customizable templates.
- Real-time data entry reduces admin time and improves accuracy, while ensuring all team members stay informed of progress.
3. Real-time inventory management prevents stockouts and overstock
- A CMMS allows you to track every spare part in real-time.
- QR codes and barcodes make it easy to log parts in and out of inventory, while automated alerts prevent critical components from going out of stock.
- Parts can be linked directly to specific assets, ensuring you maintain the right stock levels.
4. Preventive maintenance reduces unplanned downtime and failures:
- A CMMS helps to prevent breakdowns before they occur. The system schedules maintenance based on specific conditions like usage hours, meter readings, or operational triggers.
- When issues are identified, automated corrective actions ensure they’re addressed quickly.
- Reducing downtime in this way can bring big financial benefits: research shows that an hour of downtime costs $39,000 for FMCG companies and over $2 million for automotive ones.
5. Automated documentation simplifies regulatory compliance
- Smart checklists with built-in validations ensure maintenance procedures meet industry standards like GXP compliance.
- The system automatically documents all activities, creating detailed audit trails.
- Critical safety steps must be completed before work can proceed, ensuring compliance with protocols.
By centralizing information and automating key processes, CMMS transforms maintenance from a reactive cost center into a strategic asset for your organization. Teams spend less time on paperwork and more time on actual maintenance, improving overall operational efficiency.
The essential features of a CMMS
A high-quality, modern CMMS comes with a number of key features that work together to improve the efficiency and effectiveness of maintenance operations.
Let’s explore the most important ones to look for in your CMMS:
- Work orders: Any CMMS should have a work order management system with:
- Smart checklists and automation, ensuring tasks meet industry standards.
- Customizable templates supporting different types of maintenance work.
- Intelligent forms to guide technicians through complex tasks, reducing errors and documentation time.
- Asset management: A CMMS should allow all equipment data, maintenance history, and related documents to be stored in one searchable location. Teams should be able to quickly access critical information, track repairs and inspections, and make data-driven decisions about maintenance strategy.
- Planning and scheduling: Drag-and-drop scheduling, skill-based assignment, and multi-level planning capabilities help you to optimize how you use your workforce. These features manage shifts, absences, and schedules while tracking workforce availability in real-time. This ensures the right technicians are assigned to the right jobs at the right time.
- Spare parts and inventor: Real-time inventory tracking is an essential feature to ensure you always have critical parts when needed. QR code scanning simplifies parts management, while automated alerts prevent stockouts. The system helps maintain optimal stock levels, reducing excess inventory costs while ensuring parts are available for scheduled maintenance tasks.
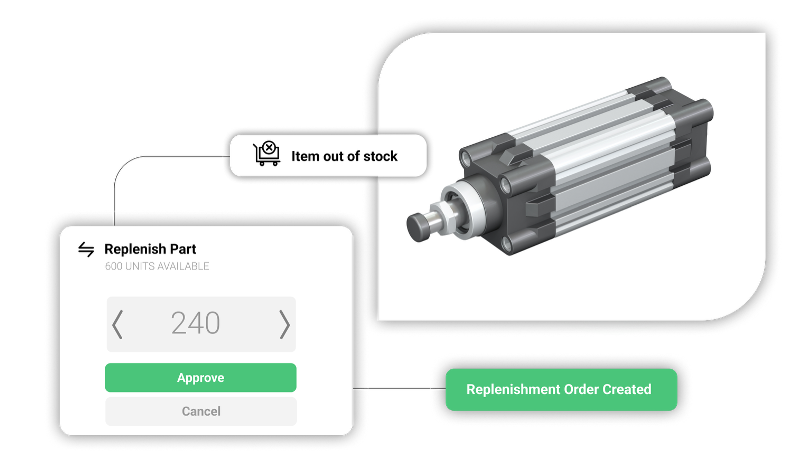
- Preventive maintenance: A high-quality CMMS enables preventive maintenance of your assets. Automated repairs and follow-up tasks, real-time progress tracking, ensure maintenance stays on schedule and issues are addressed quickly. This approach helps prevent equipment failures before they occur, allowing assets to last longer and reducing unexpected downtime.
We acknowledge we may be a bit biased, as these are the features that our osapiens CMMS offers. But we genuinely believe that these are the capabilities you need to have an efficient, modern maintenance platform.
CMMS in practice: industry examples
Let’s look at some examples of how different industries use CMMS features to solve their specific maintenance challenges.
In the food and beverage industry, where contamination risks and regulatory requirements are high, a CMMS proves invaluable. Smart checklists ensure maintenance procedures follow strict hygiene protocols, while automated documentation helps maintain compliance. The preventive maintenance features are particularly crucial – scheduling routine equipment cleaning and calibration during planned downtimes helps prevent the costly product spoilage and waste that plague this industry.
Pharmaceutical industry maintenance teams face uniquely stringent compliance requirements and documentation needs. A CMMS helps manage this complexity by enforcing qualification checks for technicians, maintaining detailed maintenance histories for audits, and ensuring all procedures follow validated protocols. The system’s ability to automatically generate compliant documentation saves countless hours while reducing compliance risks that could impact drug quality and safety.
For energy and utilities providers, equipment failure is costly and can leave entire communities without power. A CMMS helps maintain critical infrastructure through condition monitoring and preventive maintenance scheduling. The system’s real-time equipment status updates and automated work order generation ensure issues are addressed before they escalate into damaging outages.
Looking forward: exciting innovations in CMMS solutions
The next generation of CMMS solutions is being shaped by new technologies and approaches that promise to make maintenance even smarter and more efficient:
- The flexible, “start small and scale” approach is replacing big, risky projects with clunky software. Modern CMMS solutions allow teams to first implement them on a smaller scale and then scale their use once their value is proven.
- End-to-end process automation through integrations. For example, automated spare part ordering when stock levels are low, triggered through a direct connection to your procurement system or CRM.
- IoT and sensor data integration enable advanced equipment monitoring and true condition-based maintenance. Through integration with smart sensors, maintenance teams can continuously collect real-time data on temperature, vibration, pressure, and other critical metrics. When integrated with the CMMS, this sensor data triggers alerts and work orders based on actual equipment conditions and usage, moving beyond simple time-based schedules to a more proactive approach.
- AI and machine learning can analyze patterns in equipment performance data and forecast potential failures before they occur. This means maintenance teams can intervene at exactly the right time – not too early (wasting resources) or too late (risking breakdown).
Commenting on how we’re implementing AI at osapiens, our Head of Growth, Florian Bartholomäus, said: “We’re working on suggestion features that show the operator the right info based on past work orders, asset condition, and other factors. The idea is to make it easier to get the job done right and reduce errors.”
These emerging technologies are already allowing maintenance teams to take predictive maintenance to a new level and will only continue to improve rapidly.
Making the right choice of solution
Before selecting a CMMS, evaluate your current challenges. Are manual processes causing delays? Is equipment downtime affecting production? Do you lack visibility into maintenance histories and spare parts? Understanding these pain points will help you identify the features that matter most for your operation.
Modern CMMS solutions should offer quick implementation, scalability, and complete coverage of all maintenance processes. Look for cloud-based platforms that don’t require you to have expensive IT infrastructure and integrate smoothly with your existing systems. Most importantly, ensure the solution can grow with your organization’s needs.
Why choose osapiens HUB for Maintenance
The osapiens HUB for maintenance increases uptime with a wide range of features to plan, track and automate maintenance tasks:
- Single source of truth for instant access to centralized maintenance history and data
- Smart work orders with built-in checklists and validations for audits, inspections, safety procedures, and training
- Real-time spare parts tracking with automated alerts
- Preventive maintenance scheduling to reduce downtime
- Automated documentation for regulatory compliance
- Mobile access for your maintenance teams
The modern, cloud-based approach that osapiens HUB for Maintenance offers means implementation is quick and easy – no lengthy IT rollouts or complex backend integrations required. Key advantages include:
- No infrastructure overhead – all maintenance, updates, and backups included
- Highly flexible and scalable – start small and expand as needed
- End-to-end coverage – manage your entire maintenance operation in one platform
Try osapiens HUB for free today or book a demo to see how we can help improve your maintenance operations.