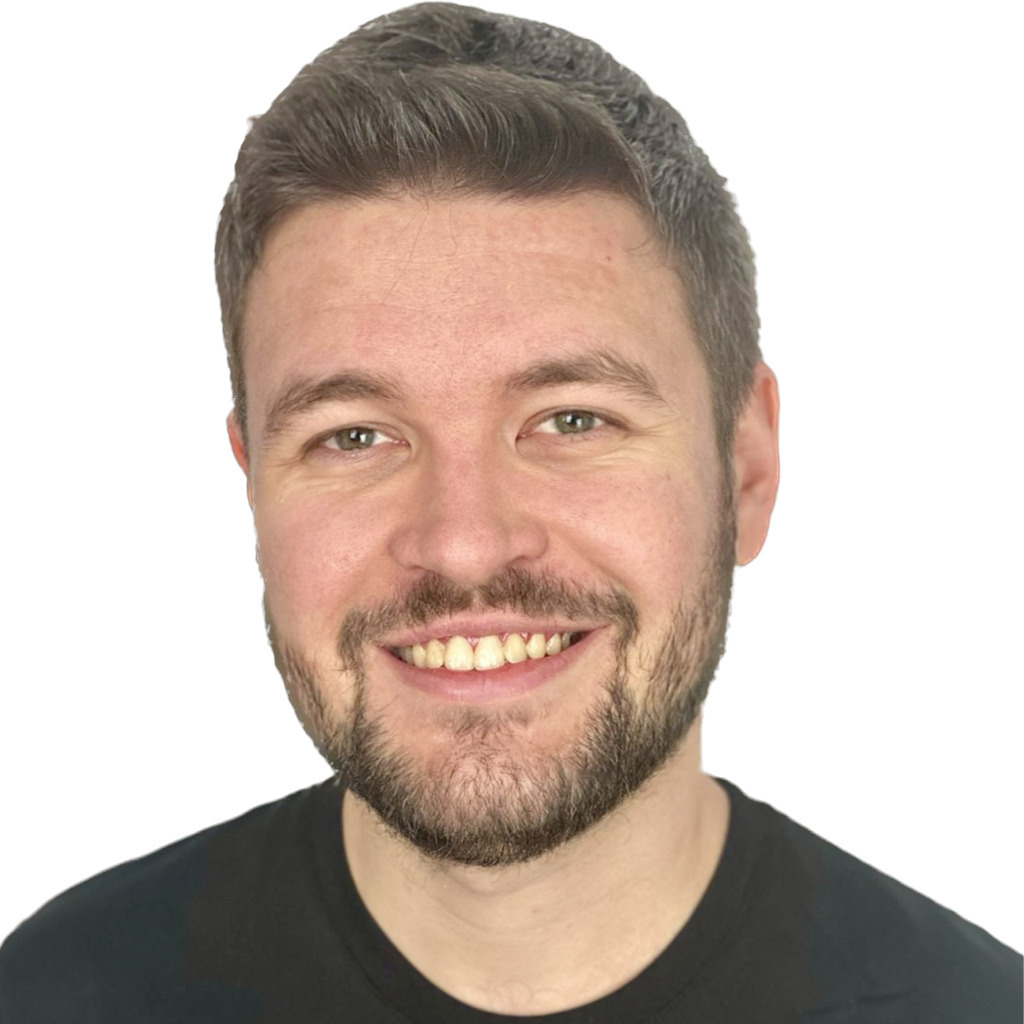
Denis Oschepkov
April 25, 2025 | Read time 5 min.Remaining Useful Life (RUL) refers to the estimated time period during which equipment or components can continue to operate efficiently and safely before they fail or need replacement. Accurately determining RUL is crucial for a modern, data-driven maintenance strategy, as it helps companies to avoid unplanned downtime, reduce maintenance costs, and maximize the lifespan of machinery and equipment.
In contrast to rigid maintenance schedules based on manufacturer specifications or past experiences, RUL enables a dynamic maintenance strategy. By continuously monitoring machinery and utilizing data analysis and predictive algorithms, companies can precisely determine the optimal maintenance timing.
Why is calculating RUL important?
Traditional maintenance strategies are either based on fixed maintenance intervals (preventive maintenance) or respond only when defects occur (reactive maintenance). Both approaches have disadvantages:
- Reactive maintenance: leads to unplanned downtime, high repair costs, and potential safety risks.
- Preventive maintenance: may result in components being replaced before it is actually necessary, increasing costs and maintenance effort.
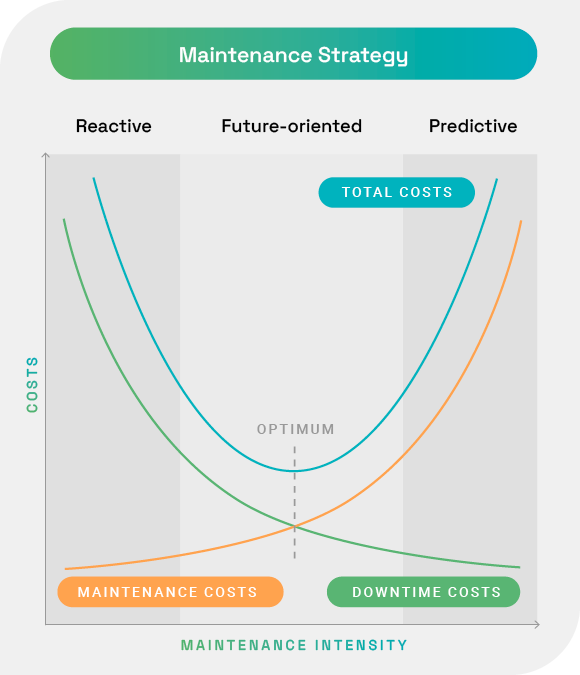
The implementation of an RUL-based maintenance strategy combines real-time data, AI-driven analyses, and sensor monitoring to make more precise maintenance decisions.
Advantages of an RUL-based strategy:
- Reduced downtime: Early warnings prevent unexpected machine failures.
- Optimized maintenance planning: Maintenance is performed precisely when needed.
- More efficient resource utilization: Labor time, spare parts, and maintenance costs are minimized.
- Extended machine lifespan: Damage can be proactively avoided.
How is Remaining Useful Life (RUL) calculated?
The calculation of RUL involves several steps and is based on the combination of various data sources, algorithms, and analytical methods.
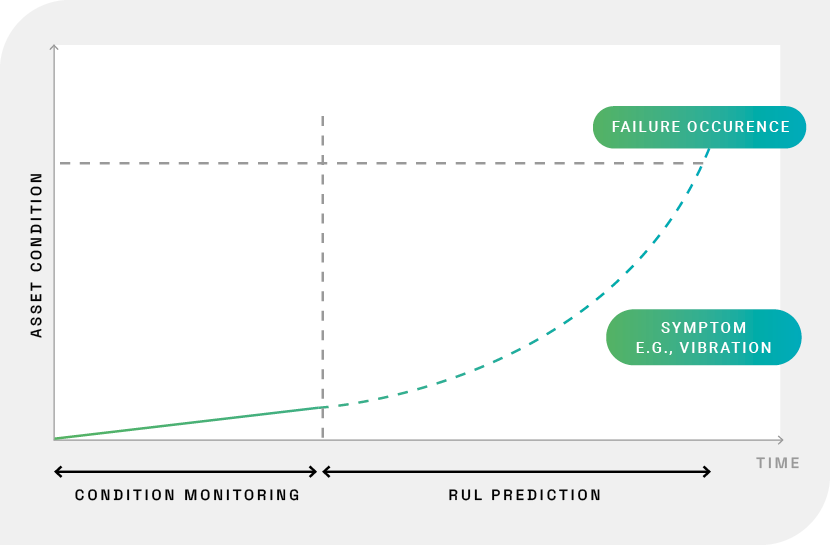
- Data Integration and Analysis: CMMS systems (Computerized Maintenance Management Systems) collect data from various sources such as IoT sensors, maintenance documentation, and operational information. This data is utilized to create models for life expectancy predictions.
- Condition Monitoring: Real-time monitoring of vibrations, temperatures, pressure, oil quality, and other relevant machine parameters. The system analyzes deviations from normal conditions and detects early signs of wear or defects.
- Predictive Analytics & Machine Learning: Algorithms identify patterns in historical and real-time data. The system predicts when a component is highly likely to fail. Maintenance activities are dynamically planned before a failure occurs.
- Automated Maintenance Scheduling in CMMS: Once the calculated RUL reaches a critical threshold, a maintenance order is automatically generated. Maintenance managers can make targeted decisions regarding whether a replacement or repair is necessary.
RUL vs. Asset Life – What’s the difference?
The terms Remaining Useful Life (RUL) and Asset Life are often confused but refer to different concepts in maintenance.
Asset Life: The total lifespan of an asset
Asset Life or total lifespan refers to the period in Enterprise Asset Management from the commissioning of an asset or machine until its final decommissioning or replacement. This period is based on manufacturer specifications, design criteria, and practical experience, and is often considered the theoretical lifespan.
Example: A manufacturer states that an electric motor has an expected lifespan of 20 years.
However, the actual lifespan can vary significantly depending on:
- Operating conditions (e.g., load, environmental factors)
- Maintenance strategy (reactive, preventive, predictive)
- Quality of spare parts and repairs
Remaining Useful Life (RUL): The predicted remaining lifespan
The Remaining Useful Life (RUL) indicates how long an asset or component is expected to remain functional based on its current condition before a failure occurs or replacement is required.
Example: Sensor data detects that an electric motor is operating at higher-than-usual temperatures. An algorithm predicts that the motor’s bearing may fail within the next 500 operating hours.
Unlike the static Asset Life, RUL is based on real-time and historical data, allowing for more accurate predictions.
Comparison: Asset Life vs. Remaining Useful Life (RUL)
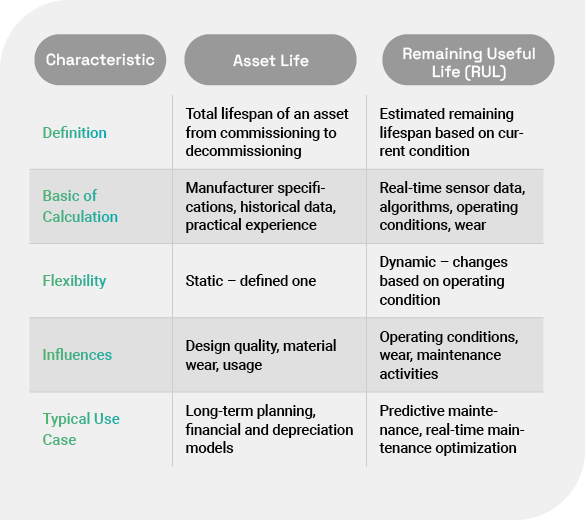
Practical Example of RUL Application:
An industrial company uses a CMMS to monitor the vibration levels of motor bearings in a production line.
- Real-time monitoring: Sensors measure vibrations in real time and detect anomalies.
- Remaining lifespan prediction: The system predicts the remaining useful life (RUL) of the motor bearings based on historical and current data.
- Automated maintenance planning: As soon as the RUL falls below a critical threshold, a maintenance order is automatically generated.
This prevents unplanned motor failure and ensures uninterrupted operation of the production line.
Conclusion: Why RUL is Essential for Modern Maintenance
Remaining Useful Life (RUL) is a key component of a modern, data-driven maintenance strategy and offers companies numerous advantages:
- More precise maintenance decisions: Maintenance takes place exactly when needed – not too early and not too late.
- Higher operational efficiency: Scheduled maintenance reduces production downtime and lowers long-term costs.
- Optimized spare parts planning: More accurate predictions help minimize inventory and enable targeted procurement.
CMMS systems with integrated RUL analysis enable predictive maintenance, reduce unplanned downtime, and maximize asset lifespan. As such, the predictive use of RUL makes a decisive contribution to increasing efficiency and reducing costs in maintenance.