Many pharmaceutical manufacturers still rely on paper-based processes and disconnected systems to manage their maintenance activities. In an industry where compliance is non-negotiable, this creates unnecessary complexity and risk.
Auditors expect full traceability. Maintenance teams are expected to follow GMP protocols to the letter. Yet in practice, technicians often work with incomplete data, duplicate work across systems, or rely on manual documentation in regulated environments like cleanrooms.
This doesn’t just harm compliance – it also increases costly downtime. As IDS-INDATA’s research reveals, outdated operational technology is one of the top causes of downtime, and the pharmaceutical industry faces between £500 million and £1 billion in projected losses in 2025.
This article explores why legacy systems make GMP compliance harder and more time-consuming than it needs to be, and sets out how pharma manufacturers can regain control with a mobile, audit-ready CMMS.
How inefficient processes make pharma compliance costly and difficult
Pharmaceutical manufacturers operate under strict regulatory oversight, with requirements such as GMP, FDA 21 CFR Part 11, and ISO standards defining how maintenance must be documented and executed. Despite this, many teams still use paper forms, spreadsheets, or outdated software that offers limited traceability.
These outdated processes introduce gaps that make inspections more difficult and slow down day-to-day maintenance. Even well-resourced companies with SAP often struggle with visibility, integration, and consistency across teams.
Where things go wrong
- Maintenance records are stored in folders or separate systems, making it hard to demonstrate compliance during audits
- Work orders are printed and filled out by hand, then manually entered into SAP or quality systems
- Technicians in cleanrooms have no access to digital documentation or spare parts lists
- Preventive maintenance tasks are delayed due to a lack of reminders or unclear ownership
- There is no reliable audit trail of who did what, when, or why
These issues do more than frustrate technicians. They delay maintenance, increase risk during inspections, and contribute to unplanned downtime.
In one example shared by a customer, a technician had to leave a cleanroom, remove protective clothing, and walk to another building simply to check a document. The interruption cost more than 30 minutes before any repair work could begin.
What’s more, regulators are making it clear that pharma companies must guarantee that they have effective maintenance processes. For example, a recent FDA letter orders the recipient to implement “routine, vigilant operations management oversight of equipment” with “prompt detection of equipment performance issues, effective execution of repairs, and adherence to appropriate preventive maintenance schedules.” When maintenance documentation fails, products are classified as adulterated under FDA regulations.
A framework for better, compliant pharma maintenance
So it’s clear that pharma manufacturers need to embed compliance into their daily maintenance activities – while minimizing operational inefficiencies.
A modern CMMS makes this possible by digitizing documentation, connecting systems, and enabling real-time access on the shop floor and in the cleanroom.
Here are five practical areas where pharma teams can use a CMMS to build a more compliant and efficient maintenance process.
1. Digitize audit trails and documentation
Regulations such as 21 CFR Part 11 require secure, traceable records. A CMMS ensures that all maintenance activities are automatically recorded and time-stamped, with clear attribution to users. This includes electronic signatures, change logs, and approval workflows.
Digital records reduce the risk of human error and eliminate the need to manually file and retrieve paper documentation during inspections. Everything is centralized, searchable, and audit-ready.
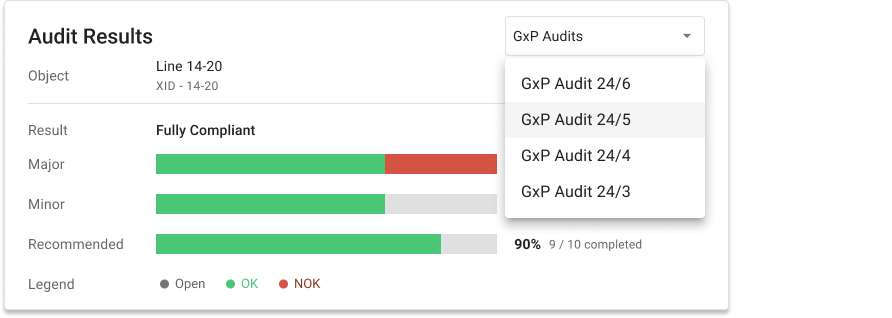
2. Enable mobile-first maintenance, even in cleanrooms
Technicians often need to access information inside regulated environments, but few systems are designed to support this. A CMMS with offline mobile functionality allows maintenance teams to view and complete work orders, check spare parts availability, and record tasks without leaving the cleanroom.
This removes delays caused by walking back and forth to offices or terminals and supports real-time compliance in highly controlled environments.
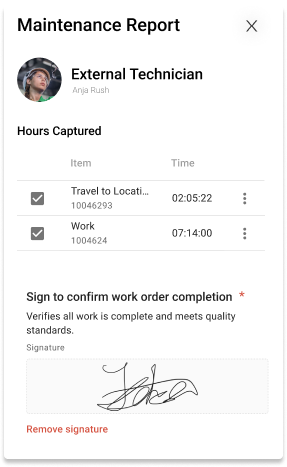
3. Standardise SOPs and automate workflows
A CMMS allows teams to embed standard operating procedures directly into maintenance workflows. Each task can include predefined steps, checklists, and validation rules to ensure consistency. Recurring tasks can be scheduled automatically, reducing the risk of missed preventive maintenance.
This improves reliability and ensures that every technician follows the same approved process, even across multiple teams or sites.
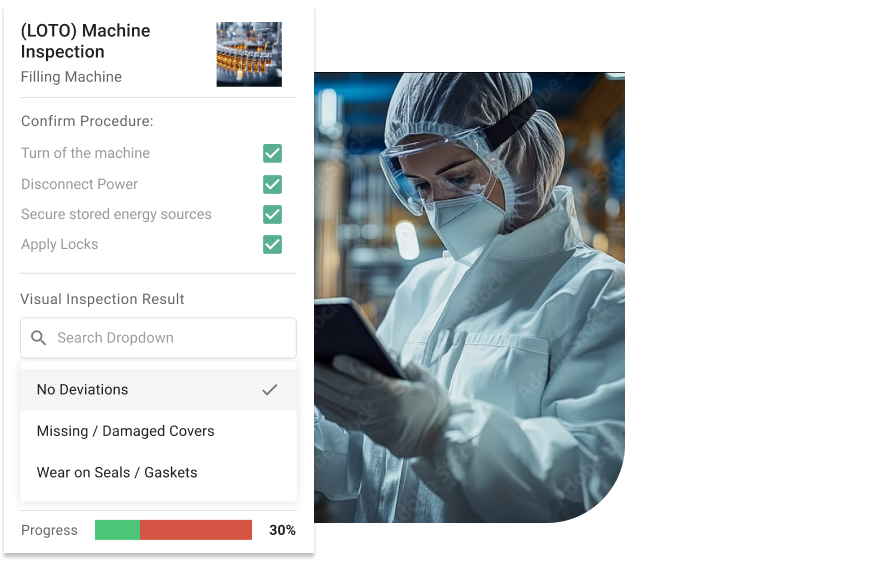
4. Integrate with SAP without complexity
Many pharma companies use SAP for asset management and procurement, but it is not designed for day-to-day maintenance execution. A CMMS that integrates smoothly with SAP allows maintenance and procurement teams to share information without duplicating work.
This means technicians can complete work orders, record parts consumption, and trigger stock updates without leaving the CMMS, while SAP continues to handle purchasing and finance.
5. Validate the system efficiently
Pharma companies cannot just install a CMMS and begin using it straight away. Regulatory expectations require full validation of the system and its processes, including IQ, OQ, and PQ stages. This is often where projects stall.
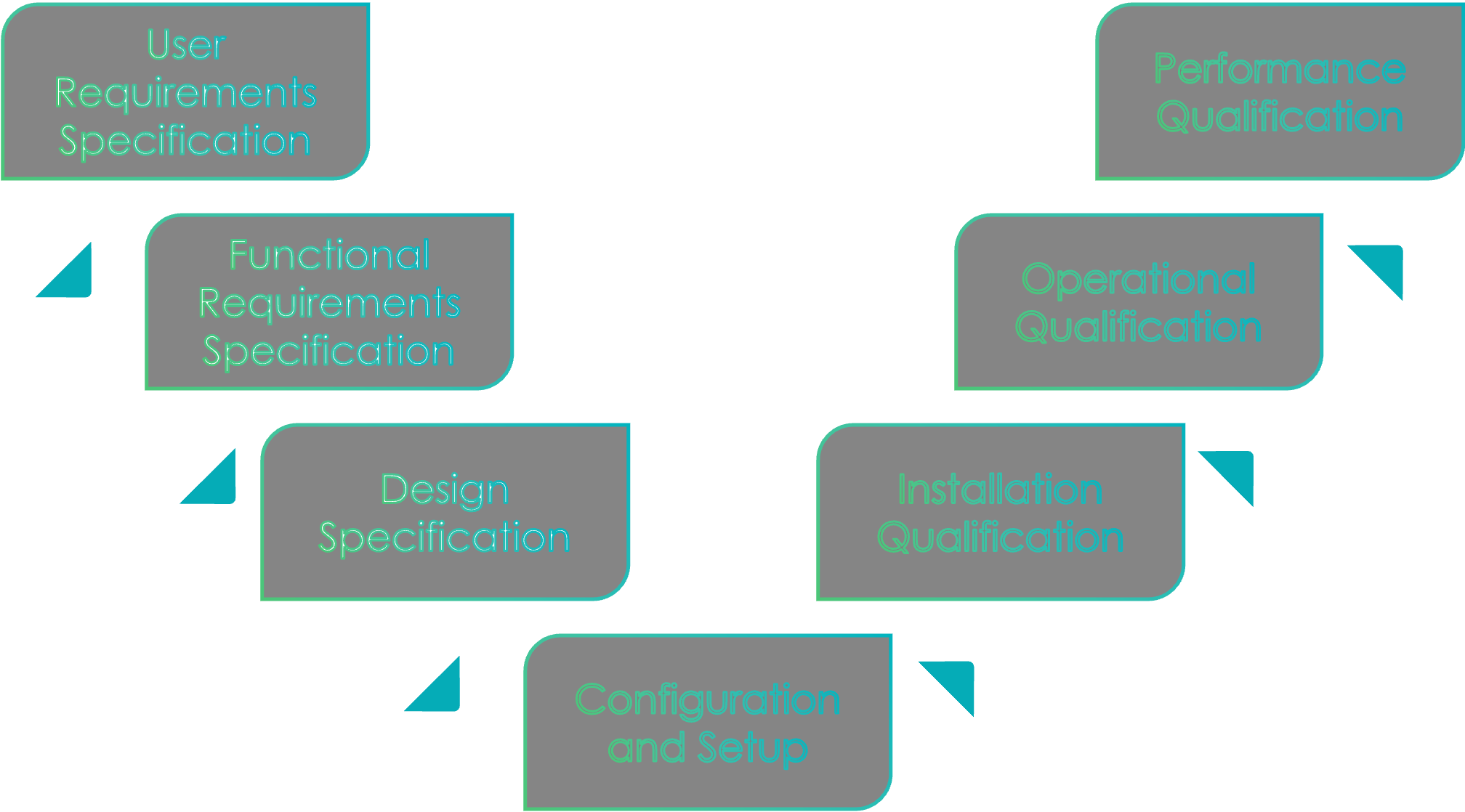
osapiens supports a lean but thorough validation approach in two key ways:
- A built-in validation framework includes pre-tested pharma workflows, predefined qualification steps, and standardised test plans. This significantly reduces the number of test cases required during validation, helping projects move forward without delay. Our validation projects can be completed in as little as three to six months.
- For companies without in-house validation expertise, osapiens offers access to a network of trusted validation partners. These experts support the qualification process and ensure that implementation meets all required GMP and 21 CFR Part 11 standards.
Together, these resources help manufacturers validate with confidence while reducing internal workload and avoiding unnecessary bottlenecks.
Why usability and SAP integration are essential
Many pharma maintenance teams find themselves stuck between two extremes. On one side are tools that are technically compliant but difficult to use. On the other side are apps that are user-friendly – but do not meet regulatory or company requirements.
osapiens CMMS is designed to be both compliant and easy to use. It combines a clean, mobile-first user experience with powerful integration capabilities for SAP systems such as S/4HANA and ECC.
This balance matters for two reasons:
- Technicians need fast, intuitive tools that support their daily work without slowing them down. Usability becomes especially important when managing tasks in cleanrooms or on the production floor, where every step counts.
- Enterprise IT and quality teams need structured, auditable processes that align with internal policies and regulatory expectations. Integrating with SAP ensures that maintenance activity is aligned with procurement, finance, and asset records – without forcing duplicate entry or custom workarounds.
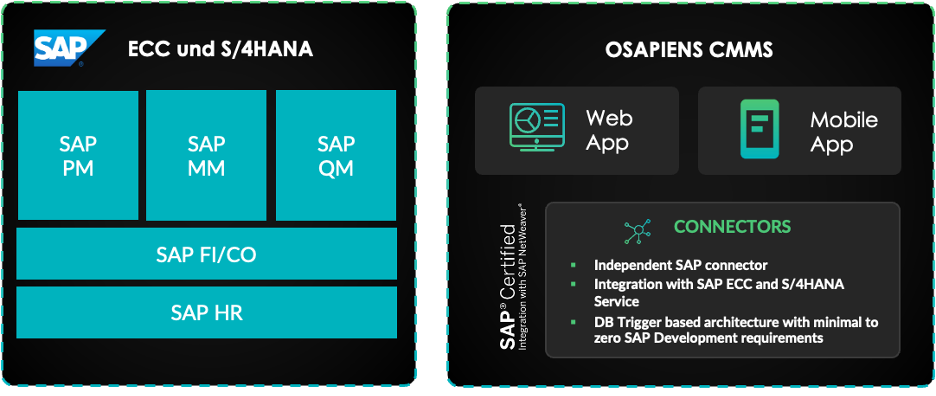
By delivering both, osapiens CMMS allows manufacturers to roll out consistent maintenance processes across teams and sites, without sacrificing compliance or slowing down daily operations.
Build compliance into the process with osapiens CMMS
In pharma manufacturing, compliance is not optional. But it should not come at the cost of slow, manual workarounds that frustrate technicians and hold back operations.
osapiens CMMS is built to make compliance part of everyday maintenance, not a separate burden. It helps pharma teams:
- Maintain clean, auditable records
- Standardise workflows across teams and sites
- Access documentation and inventory in real time – even in cleanrooms
- Reduce the time spent on administration and rework
- Move faster without compromising traceability or validation

Whether you are managing maintenance in one facility or coordinating across global sites, the right digital foundation helps ensure compliance, efficiency, and control.
Get in touch today to book a personalised demo and see how osapiens can help your team reduce audit risk, save technician time, and improve compliance readiness – without adding complexity.